New Study by Electra on Integrated EV Battery Materials Facility
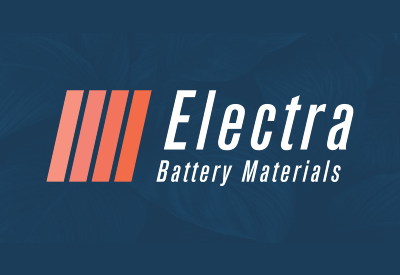
September 14, 2022
Electra Battery Materials Corporation recently released highlights of a scoping study prepared by a global engineering firm supporting the creation of an integrated electric vehicle battery materials park in Ontario that would include nickel, cobalt and manganese refining, recycling of battery black mass material, and precursor cathode active material (pCAM) manufacturing.
The scoping study assessed the economics and carbon footprint of various nickel feed options to develop an integrated facility producing 10,000 tonnes per annum of battery grade nickel sulfate and nickel equivalent pCAM, components essential to production of electric vehicle batteries. All amounts are in U.S. currency unless otherwise noted.
“With U.S. electric vehicle manufacturers moving swiftly to reduce reliance on Chinese and Russian critical minerals in order to qualify for the $7,500 EV credit under the Inflation Reduction Act, Electra is capitalizing on the opportunity to provide secure domestic supply of EV battery materials,” said Trent Mell, CEO of Electra Battery Materials. “The scoping study supports our view that an integrated refining-recycling-pCAM battery materials complex in Ontario would deliver compelling economics, emit low carbon emissions and address the onshoring of battery materials needed by the North American automotive industry.”
Mr. Mell added, “Backed by compelling project economics, we are now proceeding with an engineering prefeasibility study to narrow our focus on feed sources and devise a multi-phased approach to growing nickel refining capacity in North America.”
Scoping Study Highlights and Project Economics
- The scoping study examined the construction of a battery grade nickel sulfate refinery in Ontario by 2025-26, with three feed base loads: nickel sulfides, Class 1 nickel metal and ferro nickel, supplemented with recycled battery black mass and nickel-rich mixed hydroxide precipitate (MHP).
- Capital costs to build an integrated facility producing 10,000 tonnes per annum of nickel sulfate and nickel equivalent pCAM materials are anticipated to be between $550 and $650 million.
- Operating costs to produce 10,000 tonnes per annum of nickel sulfate and nickel equivalent pCAM materials on an integrated basis are anticipated to be between $125 and $133 million per year or between $13,000 and $13,600 per tonne of nickel sulfate produced (excluding byproduct credits), configured for NMC 811 EV battery chemistries.
- The integrated production facility is expected to contribute $225 million of GDP impact during the construction phase, including $112 million of salaries and $35 million of taxes plus an additional $415 million during the first 10 years of operations, including $111 million of salaries and $78 million of taxes.
- The integrated facility will utilize a hydrometallurgical flowsheet and leverage Electra’s emerging expertise and permitted refining complex.
- 10,000 tonnes of per annum production of battery grade nickel sulfate and nickel equivalent pCAM could support domestic manufacturing of up to 250,000 fully electric vehicles per year.
- China refineries account for approximately 75% of battery grade nickel sulfate today.
“The benefits of an integrated recycling, refining, and pCAM facility identified by the scoping study provide a significant opportunity for Electra to further leverage its Ontario refinery location and assets,” said Electra’s VP of Engineering, Dave Marshall. “By using a phased approach towards project development and exploring collaboration opportunities for manganese and pCAM production, we will now look towards reducing capital and operating costs as we launch our engineering prefeasibility study.”