Aztec Identifies 3 Essential Specifications for Pneumatic Tubings and Fittings
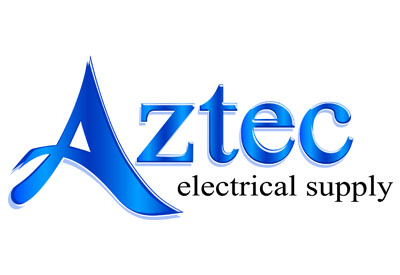
September 14, 2017
Is your industrial or manufacturing facility in Toronto adopting pneumatic automation for increased efficiency in operations? In the process, you will come across many parts necessary for pneumatic equipment to function well and serve your purposes. An essential component you will come across and choose according to your day-to-day operational needs are pneumatic tubings and fittings.
Does your team know how to select the right pneumatic tubings and fittings for your facility’s operations? Here’s a supplier’s guide to specifications of fittings and factors to consider, such as sizing, operation, and materials:
Sizing of Tubings and Fittings
The first consideration in finding the right pneumatic tubings is proper fit and sizing. Without proper sizing, oversized or undersized fittings may be selected, which can be completely incompatible with your pneumatic automation equipment, or in some cases will seal or connect inadequately – both resulting in inefficient operations or worse, malfunctioning equipment.
When determining the proper fit of pneumatic tubings and fittings, it’s important to make sure that the measurement system used in the fittings’ specifications match the equipment or assembly being fitted. Additionally, make sure that the tubes, hoses and pipes are matched to the equipment or assembly according to both the inside and outside diameter to account for both the empty portion of the cylinder, as well as the thickness of the tubing wall.
Operational Requirements
Depending on the operational requirements of your industrial or manufacturing facility in Toronto, there are different options for pneumatic tubings and fittings you can consider, based on what they are designed to handle:
- Operating pressure range: this refers to the working range of pressures or pressure ratings at which the pneumatic tubing is designed to operate, usually measured in pounds per square inch (psi). If a fitting is used in an equipment that operates above or below the pressure range, this could cause the fitting to fail, resulting in breakage, leaks, or loss of its seal.
- Operating temperature range: this refers to the appropriate range of temperatures or temperature ratings at which the fitting was designed to be used, measured in degrees Fahrenheit or degrees Celsius. When pneumatic equipment and accompanying tubings and fittings operate above or below this range, the fitting could fail.
Material Composition
No pneumatic tubings and fittings were created equally. Different material compositions determine various physical properties, as well as the compatibility of each fitting with gas to be used in powering operations.
There are generally three types of materials used in pneumatic tubings and fittings, metals, plastics, and composites:
Metals
Metals such as aluminum, brass, steel, and stainless steel are typically used in the formation of pneumatic tubings and fittings. These materials pose heat and corrosion resistance, as well as added chemical resistance and rust protection. The result is high performance evident in improved strength, machinability, and conductivity of your facility’s pneumatic automation equipment in Toronto.
Plastics
Fluouroresin polymers and polypropylene thermoplastics are also usually used in pneumatic tubings and fittings because of their suitability to extreme temperature and weather conditions; broad compatibility with different equipment and assemblies; durability; chemical resistance; and budget-friendly pricing.
Composites
Composite pneumatic tubings and fittings are made from combinations of different materials, such as carbon, fiberglass and graphite. Composites are known for having high melting points and low electrical and thermal conductivity, making them viable options for applications that require high temperature durability and chemical resistance.
Written by Aztec Electrical Supply
http://www.aztecsupply.com/3-essential-specifications-to-consider-for-pneumatic-tubings-fittings/